今回は学生の中島さんがプラスチック容器をイチから作っているシーピー化成株式会社の野村 晋史(のむら しんじ)さんに直撃インタビューしてきました。
これを読んだらあの容器達への見る目が変わること、間違いなしです!
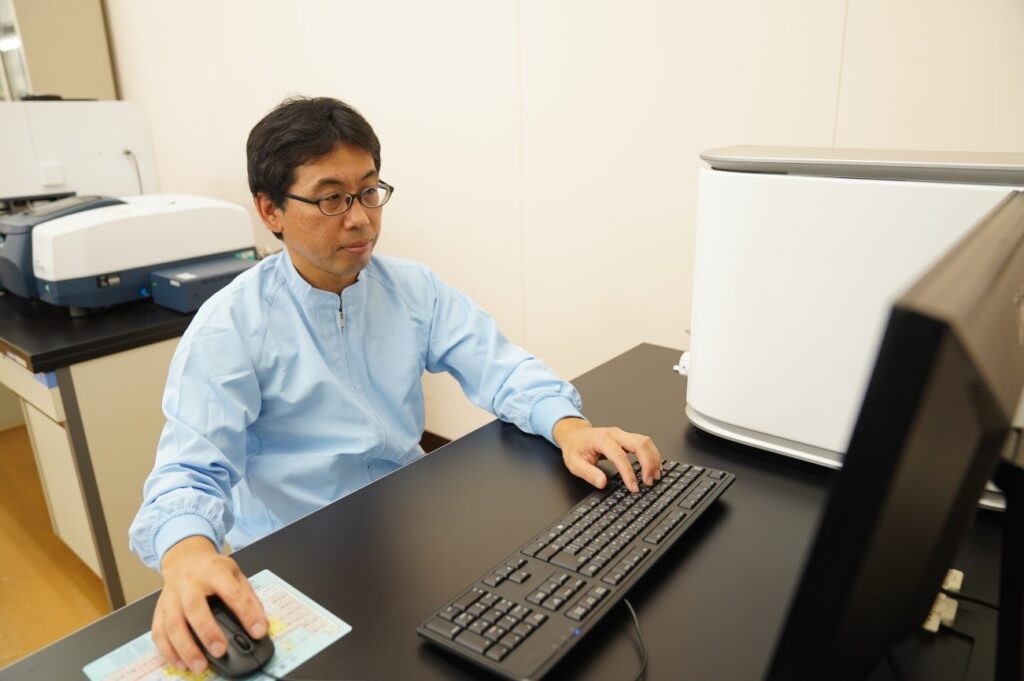
Index
岡山発、新たな食品容器を作り続けるシーピー化成
テープなしの弁当容器の生みの親
- プラスチックの食品容器といってもいろいろあると思うのですが、シーピー化成さんではどんな製品を作っているのですか?
-
野村
スーパーで売っているお弁当や惣菜などの、食品を入れる容器を作っています。用途によって様々な形状、色、柄の製品があり、その種類は8000種類にも及びます。本当に多種多様なんですよ。
ヒット製品のひとつである「リアルリーフ」。本物そっくりのリーフ柄が印刷されています!
- そんなにあるんですか!?
-
野村
ビックリしますよね。精肉や鮮魚が入っている白いトレー、屋台に並ぶ焼きそばなどが入っている透明なフードパック、お寿司などが入った柄入りの容器と、見た目も違いますし、おにぎりやサンドイッチのように中の食品にあわせた形状もありますからね。この製品の豊富さが当社の特徴の一つです。
- その中でも特に特徴的な製品はありますか?
-
野村
「強嵌合®(きょうかんごう)」という製品シリーズですね。食品容器はフタと容器の二つの部分に分かれてますが、よくその二つがテープで留めてありませんか?実はそのテープ留めが食品販売を行うお店にとってすごく手間だったんです。
当社の技術を結集してその問題を解消したのがこの製品で、テープで止めなくてもフタがしっかり閉まるという機能を実現させました。
- テープをはがしたらフタがすぐ開いてしまって困ったこと、確かにあります。この容器は便利そうですね!
豊富な種類の秘密はどこにある?
- シーピー化成さんが8,000種類も製品を作れたのには何か秘密があるんですか?
-
野村
それはお客様の課題やニーズに対応するため素材研究から製品デザイン、製品化するための生産設備や製造機器の開発、これらを自社で手掛ける「一貫生産体制」があるからなんです。食品容器がどのように作られるか、中島さんは見たことがありますか?
- えっ、そういえばないです…
-
野村
そうですよね、こちらをご覧いただくと分かりやすいかな。
まず、プラスチックの食品容器の製造工程は大きく「押出」「成形」「プレス」の3つに分かれています。最初の「押出」は樹脂の原料を溶かして平べったいプラスチックのシートを作り、それをロール状に巻き取って容器のもとになる材料を作る工程です。
- すごく大きなトイレットペーパーみたいですね…!
-
野村
見えますね(笑)。このまっさらなシートを容器の形が並んだ金型で挟みこみ、容器の形をつける工程を「成形」といいます。さらに容器を一つひとつ切り分けて、検査・包装・梱包まで行うのが「プレス」という工程です。
食品容器業界ではシートは自社で作らず「成形」段階から容器を作る企業が比較的多いんですよ。
- シートから作ることにメリットはあるんですか?
-
野村
食品容器の厚み、形状、色はシートの素材によって大きく変わります。お客様の要望に合わせてシートから作ることができれば、個別のニーズに最適化した製品を作ることができるんです。だからこそ、当社は8,000を超える製品ラインナップを用意できたとも言えます。
新素材開発と異物の分析を行う研究部門
- 野村さんは現在「押出」「成形」「プレス」のうちのどの部門でお仕事をされているんですか?
-
野村
以前はシートを製造する押出課に所属していたのですが、現在は生産本部の研究室で働いています。
業務は大きく分けて二つ、研究業務と分析業務があります。研究業務はまだ市場に出ていない新しい素材を使った容器の開発を行う仕事で、昨今は環境に配慮したバイオマスプラスチック容器の開発に力を入れています。
- 分析業務はどんなことをするんですか?
-
野村
検品中に食品容器で見つかった異物などの原因究明や再発防止などを行います。たとえば付着していた汚れの調査です。
汚れと一口に言っても、実際に顕微鏡で拡大してみると実はいろんなものが混ざっている場合が多く、とても複雑です。どこから混入したのか、なぜ混入したのか、時には1mm以下の汚れから可能な限り情報を引き出すのが私たちの役目です。
- そんなに小さいなんて、とても大変そうです。
-
野村
紛失してしまわないように非常に気をつかいますよ。ただ、私たちの分析結果が品質改善につながっていくので、やりがいは大きいです。研究も分析も一つひとつ問題に向き合い解決していくというところに醍醐味があると思っています。
現場経験で野村さんが学んだこと
「なんでもできる」は「なにもできない」?
- 野村さんは入社前と入社後でギャップを感じて悩んだことはありますか?
-
野村
ありますよ。私は大学時代に高分子化学というプラスチックに関わる学問を学んでいたので、その専門知識を活かしたいと考えシーピー化成に入社を決めました。
でも、最初に配属されたのはシートを製造する押出課でした。押出課はいかに生産計画に則って安定的にシートを製造していくかが重要な部署です。そこで求められるのはトラブルがあったときの設備復旧に必要な電気や機械の幅広い知識でした。
配属当時は「もっと専門的なことを学びたいんです!」と先輩や上司に反発しました。今思えば若かったなと思いますが…(笑)。
- 現場を知ることが大事だからまずは現場配属になるというのはよく聞きますよね。
-
野村
そうなんです。でも、私は現場経験によって「なんでもできる」という状態になることは、相対的に見れば突出した専門性のない「なにもできない」人材になってしまうことではないかと強い不安を抱いていたんです。
実際、研究部門に入った今は製造現場で学んだ電気や機械の知識が非常に役立っていて必要な経験だったなと実感できています。あの頃の私の気持ちを受けとめてくださった当時の先輩と上司には本当に感謝しかありません。
問題解決っておもしろい!
- 製造現場にいた頃で、今も思い出す印象的なエピソードはありますか?
-
野村
まだ入社間もない頃に起きたトラブルのことをよく思い出しますね。
シートを作る際は様々な素材を取り扱うため、生産予定に合わせて、都度原料を入れ替えることになります。この原料を入れ替えた後の機械立ち上げ時には、必ず製品にならないスクラップが出てしまうもので、この製造ロスを一定幅に管理する必要があります。ですが、そのロスが通常の2倍〜3倍の値になってしまうことがあって。
その生産記録を調査し続けたある日、特定の品種からある別の品種に組み替えたときだけその現象が起きることに気がついたんです。その組み合わせを行わないようにしたら、ピタッと製造ロスの倍増現象は起きなくなりました。
あのときの「そういうことなのか!?」という閃きの感覚は忘れられません。課題解決のおもしろさを知った瞬間でしたね。
- すごいですね!
-
野村
解決後も「なんであんな現象が起きたんだろう?」「設備の中では一体どんなことが起こっているんだ?」とずっと考えていました。これが誰も正解を知らない問題に取り組むことのおもしろさですよね。
現在は研究部門としてそのおもしろさを折に触れて感じています。新素材開発や新たなトラブルは誰も答えを知らない課題です。専門知識や経験は役には立つけれども、それだけでは解決はできません。かえって経験や先入観が邪魔をすることだってあります。
そんな中で大切なのは、若手も経験あるメンバーもそれぞれが考え自分なりの意見を交わし合うこと、そして分からないことを「不思議だ」と自分の心にマーキングして考え続けることなんです。そうしたことが「あ、そういうことか!」という瞬間につながっていく。それがとてもおもしろいんです。
野村さんの挑戦と若者へのアドバイス
- これから野村さんが挑戦していきたいことは何ですか?
-
野村
あらためて自分の専門性を深く育ていくことです。実は、まだ研究室に入って日が浅い私は、自分自身が研究者と名乗るレベルに到達しているとはおこがましくてとても思えていないんです。
入社から現場で幅広い知識と経験を得ることは必要なことでしたが、これからは「私は研究者です」と胸を張って名乗るためにも、より深く高分子樹脂を学んで自分の軸にしていきたいと考えています。
- 最後に若者へアドバイスをいただけますか?
-
野村
学生の皆さんも卒論や修論など忙しいと思いますが、どうか就職に向けて悔いが無いように勉強して専門性や熱意を高めておいてください。
ただ、就職して上司や先輩に「自分は興味が無い」と思う分野の仕事や勉強を薦められたときには、ぜひ素直に取り組んでみてください。自分の知識を幅広く増やすことも、必ず先に未来につながっていきますから。
- なるほど、頑張ります!野村さん、今日はありがとうございました!!